After working in Management roles and in corporate business for more than 25 years, I’ve seen firsthand how important it is to have clear and comprehensive standard operating procedures (SOPs) in place. I was fortunate enough to work as a kid at McDonald’s, and the company’s detailed SOPs (mainly in the form of Station Observation Checklists – SOCs) provided absolute clarity to all staff members on how to perform every aspect of their job. However, in other industries and companies where I subsequently worked SOPs were not as clear or comprehensive (if they existed at all), and I saw the negative impact this would have on training and accountability. Without clear procedures and guidelines, staff members were often left to figure things out on their own, which led to inconsistent results and inefficiencies. So, I wanted to explore the importance of having effective SOPs for businesses and provide tips for developing SOPs that can help improve efficiency and consistency as well as training and accountability across your organization.
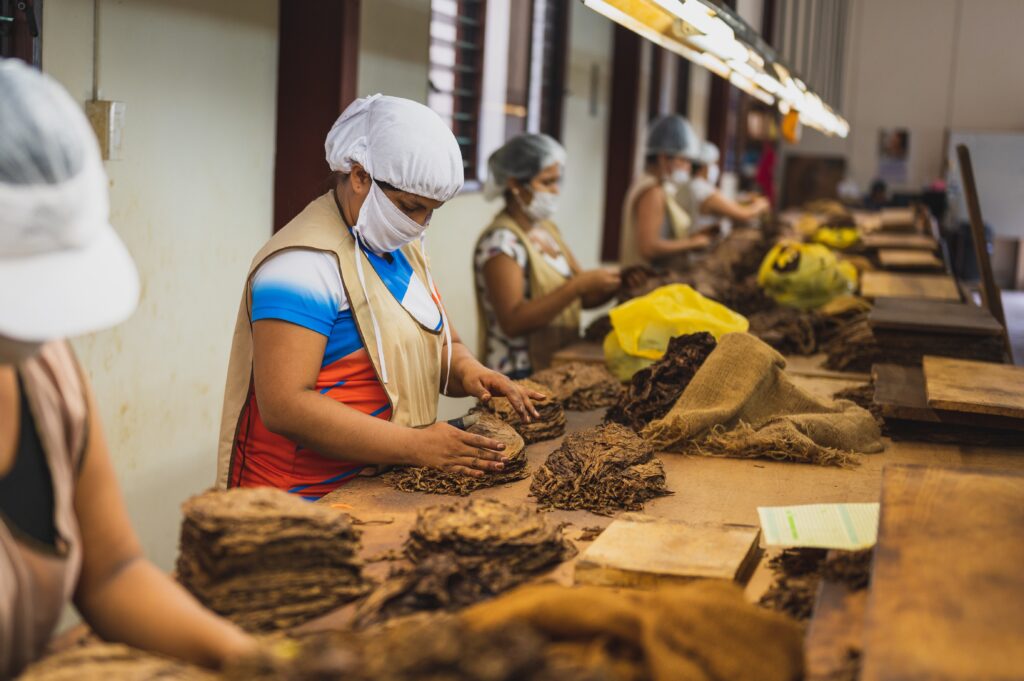
Why SOPs are Critical for Business Success
SOPs are critical for the success of any business. They are the foundation of a well-managed, efficient, and consistent operation. SOPs are step-by-step instructions that define how specific tasks should be performed in a standardized and repeatable manner. These instructions can be for anything from assembling a product to managing inventory or providing customer service.
The benefits of SOPs for businesses are many. First, SOPs help to ensure that work is performed consistently and to a high standard. With standardized procedures, employees know exactly what is expected of them and how to perform their job correctly. This helps to eliminate errors and inconsistencies, which can lead to higher quality output and customer satisfaction.
SOPs also help to increase efficiency and reduce business costs. By defining specific procedures, companies can eliminate unnecessary steps and streamline many workflows. All of this helps to reduce waste, save time, and improve productivity.
Another benefit of SOPs is that they can help to ensure health & safety procedures are followed and so reduce risk for the business and particularly for staff as well as clients & customers. By clearly outlining safe working procedures and potential hazards, companies can minimize the risk of accidents or injuries. This can help to protect employees, customers, and the business itself from harm as well as workplace health & safety and risk.
Finally, SOPs can also help to promote accountability and ensure staff are trained well. When employees know exactly what is expected of them and how to perform their job correctly, they are better equipped to take ownership of their work and improve their skills over time. If your company’s operating procedures are robust & clear there’s less opportunity for staff to veer off and do their own thing when they perform various tasks, and there will be a greater ability for managers to performance manage staff who attempt to do so. SOPs also provide a useful training tool for new employees, making it easier to onboard new staff members and ensure they are fully trained and capable of performing their job to a high standard.
In short, SOPs are critical for businesses of all types and sizes. They help to ensure consistency, quality, efficiency, safety, and accountability across all operations. Without effective SOPs, companies may struggle to meet their goals, maintain their competitive edge, and ensure customer satisfaction.
Tips for Developing Effective SOPs
So, it should be clear that developing effective Standard Operating Procedures (SOPs) is critical for the success of any business because effective SOPs can help to ensure consistency, efficiency, safety, and accountability across all operations. Here are some guidelines for developing effective SOPs:
- Identify the process: You first need to identify the process or task that needs to be documented. It’s important to understand the steps involved and the people who are involved in the process.
- Define the purpose: You then need to clearly define the purpose and objective of the SOP, and specify the desired outcome or goal. It’s important to understand the context and the reason behind the process.
- Gather information: Once you’ve identified the process which needs to be documented, and defined the objective of the SOP, you then will need to gather information from various sources, including employees who perform the task, supervisors and/or managers who oversee the staff performing the task, as well as any other subject matter experts even from other company departments, and any relevant documentation the business may already have.
- Create an outline: Once you’ve gathered all the information on how to perform the task, create an outline of the procedure that includes all the steps involved in the process, along with any relevant sub-steps. Make sure the outline is easy to read and understand. There are 2 main groups or sorts of people that I think of as the target audience, first is the staff who perform the task, and the second is the team members that would ordinarily train these staff members. These 2 types of employees need to be able to follow the SOP document easily.
- Draft the SOP: Use the outline to draft the SOP. The SOP should include all the information necessary to complete the process, including step-by-step instructions, diagrams, and any relevant forms or templates.
- Review and revise: Thoroughly review the SOP first with employees who perform the task, then secondly with the various subject matter experts who provided valuable information in the ‘gather information’ step for the SOP. Once you’ve reviewed the SOP with these groups of people, revise the SOP as needed to ensure it’s accurate and effective.
- Approve and publish: Finally, obtain approval from management or other relevant stakeholders, and publish the SOP in a centralized location where employees can access it easily.
By following these guidelines, businesses can develop effective SOPs that improve efficiency, consistency, and accountability across all operations. It could be added as an 8th step, but updating and maintaining SOPs is an important consideration. It’s beneficial to regularly review and update the SOP as needed to ensure it remains accurate and effective. Make sure that employees are notified of any changes and that they receive updated training if necessary.
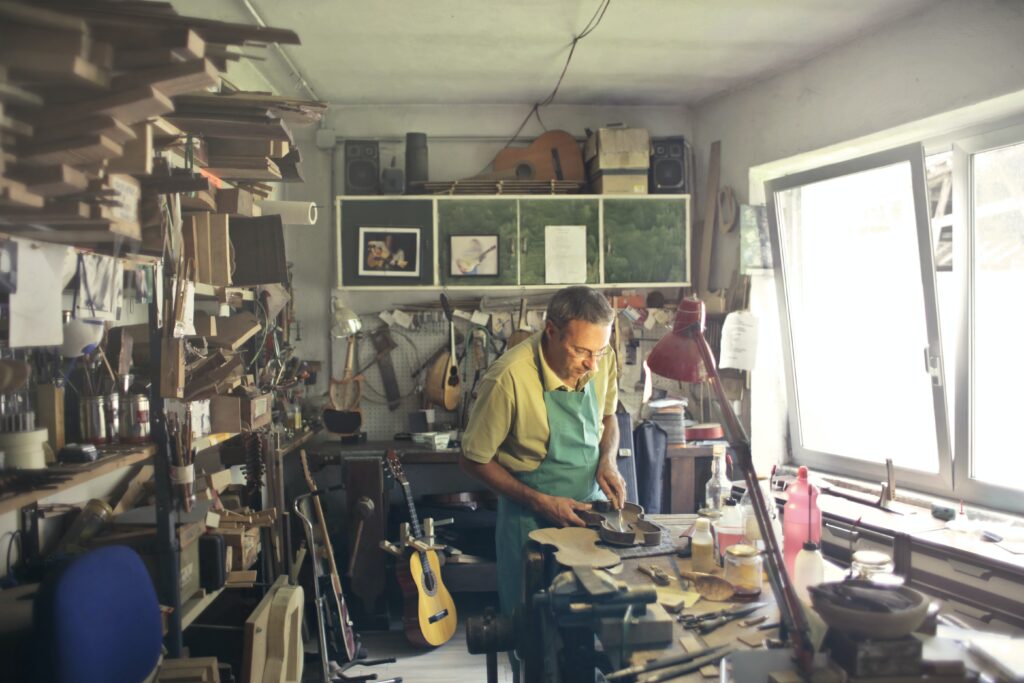
Whilst following the steps above, you may also want to consider at least some of these tips below:
- Use simple and clear language: It was implied above under step 4, but it’s important to use simple and clear language in the SOP to make it easy to understand and follow. Whenever possible, avoid technical jargon or industry-specific terms that may confuse employees. But where it makes sense to use such terms, be sure to explain them clearly.
- Keep it concise and focused: Keep the SOP concise and focused, and avoid including unnecessary information or steps that can confuse or overwhelm employees.
- Involve key stakeholders in upper management: I think this can be an optional step, although some businesses will make this mandatory. In my experience, involving key stakeholders in upper-level management can be a double-edged sword. On the one hand it can be great for considering aspects of company direction & strategy. But, on the other hand, some Senior Managers can have the tendency to want to dictate operations in other departments whilst having little to no understanding of the area of operations they’re commenting on. This can result in the creation of procedures that are not practical or realistic and can lead to frustration and confusion among employees who are tasked with implementing the procedures. And this can have follow-on effects that are also negative (disconnect between senior management and front-line employees or creating a culture of micromanagement and mistrust). If this is done well, however, it can ensure that the SOP accurately reflects the needs and requirements of the business as a whole.
- Observe the training of employees on the SOP: By observing the training of employees on the SOP, as well as ensuring trainers understand how to follow the SOP correctly it can provide opportunities for employees to ask questions and seek clarification. So, this can be one great way to test and refine the SOP with small group of employees. This will ensure that the SOP is effective in the field, and can provide real life examples of what may need to be refined based on feedback received on the job. Naturally, you can continue to update the SOP over time as conduct this testing.
How to Implement and Enforce SOPs
Once Standard Operating Procedures (SOPs) have been developed, it is important to implement and enforce them effectively. There are a few key steps to follow when implementing and enforcing SOPs:
- Communicate the SOPs: Firstly, you’ll need to communicate the SOPs to all employees who are affected by them. This can include providing training and ensuring that employees understand the purpose and importance of the SOPs.
- In doing this, particularly during training sessions, you’ll want to provide all the necessary resources you’ve created for the staff members being trained. You will also need to provide any other relevant equipment & tools both during the training and in order to carry out the task/procedure following the training.
- You’ll also want to ensure that employees have access to these resources if they need to follow up on details of the SOPs after the initial training sessions.
- Monitor compliance: This is (I think) the first of two vital steps in implementing new procedures well, you have to monitor compliance. You must do this with the SOPs to ensure that they are being followed correctly. This can involve regular checks and audits, as well as providing feedback to employees. Buy-in and oversight from Management (or Supervisor, or whoever is responsible for staff who perform the tasks outlined in the SOP) are also crucial here.
- Address non-compliance: The second of the two vital steps in implementing new procedures well is addressing non-compliance through performance management. If employees are not following the SOPs correctly, it is important to address this quickly and effectively. This should often start with providing additional (documented) training or coaching, and if non-compliance continues should then lead to disciplinary action if necessary.
Along with these key steps, it’s always helpful to keep in mind that SOPs benefit from being regularly reviewed and updated to ensure that they remain relevant and effective. You should do this more frequently in the early stages of implementation, and (hopefully) less frequently once the process is largely running smoothly and efficiently. This can involve incorporating feedback from employees to identify areas for improvement. Involving employees in the implementation and enforcement of SOPs can help cultivate a culture of ownership over the process. And this can help to promote an environment of continuous improvement and accountability.
Real-World Examples of Effective SOPs
Effective Standard Operating Procedures (SOPs) can be found across many different industries and businesses. Here are a few real-world examples:
- Toyota Production System: Toyota has long been known for its emphasis on process improvement and standardization. The Toyota Production System, which includes a number of SOPs for manufacturing, has helped the company to achieve high levels of efficiency and quality.
- Amazon Fulfillment Centers: Amazon uses a variety of SOPs to ensure that its fulfilment centres operate efficiently and effectively. These include SOPs for receiving, storing, and picking items, as well as for packaging and shipping (see below video tour).
- Healthcare: In healthcare, SOPs are used to ensure consistent and effective patient care. For example, hospitals may have SOPs for administering medications, taking patient vital signs, and responding to emergencies.
- Aviation industry: The aviation industry is known for its strict adherence to SOPs. Pilots and air traffic controllers are required to follow established procedures for takeoff, landing, and other critical operations. These procedures are designed to ensure safety and consistency across all flights.
- Food service: Restaurants and other food service businesses rely on SOPs to ensure consistency and safety. The fast-food chain McDonald’s is known for its highly effective SOPs. These procedures outline how to prepare and serve food, as well as how to manage inventory and handle customer service issues. By following these procedures, McDonald’s is able to provide consistent service and quality across all of its locations.
- Information technology: IT departments may have SOPs for tasks like managing software updates, handling security breaches, and certainly responding to service requests.
In each of these examples, effective SOPs are critical for ensuring consistent and efficient operations. By implementing and enforcing SOPs, businesses can improve productivity, quality, and customer satisfaction.
Common Mistakes to Avoid When Developing SOPs
Developing effective Standard Operating Procedures (SOPs) can be a challenging process, and there are a number of common mistakes that businesses should try to avoid. These include failing to involve front-line staff, getting the wrong balance when you outline the information contained in the SOP and you’re either too vague or too detailed, as well as failing to update the procedures when the need arises.
Another big mistake, however, is failing to honour the past. This can be a common mistake, especially in organizations with a long history or strong traditions or even strong personalities. You may neglect to look back at previous procedures and practices and fail to identify what has worked well in the past, and what can be improved or updated. Ignoring the past can lead to a lack of respect for the organization’s heritage as well, and can lead to staff members feeling disconnected from the new procedures. This can also lead to staff members being less likely to embrace the new procedures since they are developed without an appreciation for the organization’s history and values or without an appreciation of the efforts of long-serving & hard-working staff.
Having change managers who are arrogant or (worse also, even somewhat) ignorant can be a common mistake when developing SOPs. This can lead to a lack of understanding and empathy for the staff members who will be affected by the changes, and can result in procedures that are ineffective or difficult to implement. Arrogance can also lead to a lack of collaboration and consultation with key stakeholders, including staff members, and can result in a top-down approach that doesn’t take into account the real-world challenges and needs of the business. No one likes it when you have deal with a ‘know-it-all’, especially if they end up showing that they don’t know much (or anything). So, it’s important to have change managers who are open-minded, collaborative, and willing to listen to feedback from staff members and other stakeholders. This can help to ensure that the SOPs are developed in a way that is effective, practical, and tailored to the needs of the business.
Lastly, in my experience, poor planning & execution is a huge mistake when it comes to developing SOPs for a business. This could play out in the form of engaging in too much change too quickly, or there could be a lack of thoroughness in the SOP development or roll-out process. When businesses try to implement too many changes at once, or worse, there are multiple changes that need to happen because an earlier iteration was an absolute disaster, it can overwhelm staff members and lead to resistance to the new procedures. Additionally, if the SOPs are not well-planned or well-executed, staff members may not fully understand the changes or how they are supposed to implement them, which can lead to errors, confusion, and inefficiencies. It’s important to take a measured approach to implementing changes and to ensure that the SOPs are well-designed, well-communicated, and well-supported. This can help to ensure that staff members are able to adapt to the changes in a way that is effective and sustainable, leading to better outcomes for the business overall.
By avoiding at least some of these common mistakes, businesses can develop SOPs that are practical, effective, and contribute to the overall success of the organization.
Standard operating procedures (SOPs) are critical for improving efficiency and consistency within a business. By clearly documenting processes, providing guidance on how to complete tasks, and outlining expectations, SOPs can help to ensure that staff members are performing their work in a consistent and efficient manner.
However, developing effective SOPs requires careful planning, collaboration, and attention to detail. By avoiding common mistakes such as failing to engage staff members, neglecting to consider the past, or engaging in too much change too quickly, businesses can develop SOPs that are tailored to the needs of their organisation and are designed to improve both specific and overall performance. By implementing and enforcing SOPs effectively, businesses can enjoy a wide range of benefits, including increased productivity, reduced errors, and improved customer satisfaction. And by following best practices and avoiding common pitfalls, businesses can ensure that their SOPs are effective and will contribute to long-term success.